Disciplines
- MLA
- APA
- Master's
- Undergraduate
- High School
- PhD
- Harvard
- Biology
- Art
- Drama
- Movies
- Theatre
- Painting
- Music
- Architecture
- Dance
- Design
- History
- American History
- Asian History
- Literature
- Antique Literature
- American Literature
- Asian Literature
- Classic English Literature
- World Literature
- Creative Writing
- English
- Linguistics
- Law
- Criminal Justice
- Legal Issues
- Ethics
- Philosophy
- Religion
- Theology
- Anthropology
- Archaeology
- Economics
- Tourism
- Political Science
- World Affairs
- Psychology
- Sociology
- African-American Studies
- East European Studies
- Latin-American Studies
- Native-American Studies
- West European Studies
- Family and Consumer Science
- Social Issues
- Women and Gender Studies
- Social Work
- Natural Sciences
- Anatomy
- Zoology
- Ecology
- Chemistry
- Pharmacology
- Earth science
- Geography
- Geology
- Astronomy
- Physics
- Agriculture
- Agricultural Studies
- Computer Science
- Internet
- IT Management
- Web Design
- Mathematics
- Business
- Accounting
- Finance
- Investments
- Logistics
- Trade
- Management
- Marketing
- Engineering and Technology
- Engineering
- Technology
- Aeronautics
- Aviation
- Medicine and Health
- Alternative Medicine
- Healthcare
- Nursing
- Nutrition
- Communications and Media
- Advertising
- Communication Strategies
- Journalism
- Public Relations
- Education
- Educational Theories
- Pedagogy
- Teacher's Career
- Statistics
- Chicago/Turabian
- Nature
- Company Analysis
- Sport
- Paintings
- E-commerce
- Holocaust
- Education Theories
- Fashion
- Shakespeare
- Canadian Studies
- Science
- Food Safety
- Relation of Global Warming and Extreme Weather Condition
Paper Types
- Movie Review
- Essay
- Admission Essay
- Annotated Bibliography
- Application Essay
- Article Critique
- Article Review
- Article Writing
- Assessment
- Book Review
- Business Plan
- Business Proposal
- Capstone Project
- Case Study
- Coursework
- Cover Letter
- Creative Essay
- Dissertation
- Dissertation - Abstract
- Dissertation - Conclusion
- Dissertation - Discussion
- Dissertation - Hypothesis
- Dissertation - Introduction
- Dissertation - Literature
- Dissertation - Methodology
- Dissertation - Results
- GCSE Coursework
- Grant Proposal
- Admission Essay
- Annotated Bibliography
- Application Essay
- Article
- Article Critique
- Article Review
- Article Writing
- Assessment
- Book Review
- Business Plan
- Business Proposal
- Capstone Project
- Case Study
- Coursework
- Cover Letter
- Creative Essay
- Dissertation
- Dissertation - Abstract
- Dissertation - Conclusion
- Dissertation - Discussion
- Dissertation - Hypothesis
- Dissertation - Introduction
- Dissertation - Literature
- Dissertation - Methodology
- Dissertation - Results
- Essay
- GCSE Coursework
- Grant Proposal
- Interview
- Lab Report
- Literature Review
- Marketing Plan
- Math Problem
- Movie Analysis
- Movie Review
- Multiple Choice Quiz
- Online Quiz
- Outline
- Personal Statement
- Poem
- Power Point Presentation
- Power Point Presentation With Speaker Notes
- Questionnaire
- Quiz
- Reaction Paper
- Research Paper
- Research Proposal
- Resume
- Speech
- Statistics problem
- SWOT analysis
- Term Paper
- Thesis Paper
- Accounting
- Advertising
- Aeronautics
- African-American Studies
- Agricultural Studies
- Agriculture
- Alternative Medicine
- American History
- American Literature
- Anatomy
- Anthropology
- Antique Literature
- APA
- Archaeology
- Architecture
- Art
- Asian History
- Asian Literature
- Astronomy
- Aviation
- Biology
- Business
- Canadian Studies
- Chemistry
- Chicago/Turabian
- Classic English Literature
- Communication Strategies
- Communications and Media
- Company Analysis
- Computer Science
- Creative Writing
- Criminal Justice
- Dance
- Design
- Drama
- E-commerce
- Earth science
- East European Studies
- Ecology
- Economics
- Education
- Education Theories
- Educational Theories
- Engineering
- Engineering and Technology
- English
- Ethics
- Family and Consumer Science
- Fashion
- Finance
- Food Safety
- Geography
- Geology
- Harvard
- Healthcare
- High School
- History
- Holocaust
- Internet
- Investments
- IT Management
- Journalism
- Latin-American Studies
- Law
- Legal Issues
- Linguistics
- Literature
- Logistics
- Management
- Marketing
- Master's
- Mathematics
- Medicine and Health
- MLA
- Movies
- Music
- Native-American Studies
- Natural Sciences
- Nature
- Nursing
- Nutrition
- Painting
- Paintings
- Pedagogy
- Pharmacology
- PhD
- Philosophy
- Physics
- Political Science
- Psychology
- Public Relations
- Relation of Global Warming and Extreme Weather Condition
- Religion
- Science
- Shakespeare
- Social Issues
- Social Work
- Sociology
- Sport
- Statistics
- Teacher's Career
- Technology
- Theatre
- Theology
- Tourism
- Trade
- Undergraduate
- Web Design
- West European Studies
- Women and Gender Studies
- World Affairs
- World Literature
- Zoology
Is QC Better than QA or Vice Versa? Research Paper Example
Hire a Writer for Custom Research Paper
Use 10% Off Discount: "custom10" in 1 Click 👇
You are free to use it as an inspiration or a source for your own work.
Is Quality Control better than Quality Assurance or vice versa?
The meaning of quality is catering to customer requirements. A high quality product is always the one which meets the customer demands in the most efficient manner. Hence, the general needs of consumers that products should be long lasting and vulnerable to physical damage are mostly considered as signs of good quality. (Pride et al, 2011)
Quality Control is a Japanese business terminology whereby the units of outputs which are produced in a company are carefully monitored and inspected to ensure that the products being delivered to the market are up to standard and maintain quality. On the other hand, Quality Assurance is a Western technique of maintaining quality standards. Rather than inspecting and monitoring the goods for quality checks and identification of defects, Quality Assurance aims to minimize such discrepancies by simply ensuring that each and every prior step involved in the production process goes along side the standard of quality. (Beckford, 2009)
Although Quality Control aims to monitor defects and failures, Quality Assurance focuses upon elimination of these defects from the grass root level. This essay aims to present an argument if Quality Assurance precedes over Quality Control in maintenance of quality, or do both the concepts yield the same results.
Stebbing, (2009) has explained that total quality management or TQM supports both of the methods of maintaining quality and strongly emphasizes over building quality into each and every aspect of work. The TQM approach is not a simple method; rather it is a complete philosophy and way of thinking. This aspect changes the overall approach of an organization and makes sure that quality is built into the design of the product. This means utilization of minimum resources to produce maximum outputs while maintain quality. (Stebbing, 2009)
Quality Control emphasizes upon a separate QC department within a company whose prime responsibility is to keep quality checks over the overall units of output which are produced at a production facility. In most of those organizations where Quality Control departments are present, the end of an assembly line of production nearly goes to a Quality Control inspector who checks that each and every unit is catering to the quality standards. If the inspector finds any traces of defects in a particular unit of output, then that unit is rejected, which means it either goes into the trash can, or the relevant laborer who might work upon it to fix the errors and comply with quality standards. The Quality Control department might come up with occasional amendments and additions to the quality standards and in the end make it sure that all goods are complying with the quality standards in practice. There might be various ways of making random inspections for quality check. For example checking that finished goods have been packaged properly, the units inside the packaging are of a proper nature and meet the product specifications and that the quality complies with different standards already established by the management.humil The finished goods might be checked one by one or on a random basis. Similarly, semi finished or raw stock might be checked for quality and rejected or accepted based on the persistent quality standard in practice. The QC department usually hires a number of quality inspectors who main task would be to check the goods, find defects or failure to comply with quality, and reject or return them based on the relevant circumstances. (Stebbing, 2009)
On the other hand Quality Assurance, according to Aikens (2005), is a completely different technique which aims to build in quality in each and every process of production that is involved. Although this technique also evolves forming a separate quality assurance department, yet it works towards a different strategy of maintenance of quality. The quality assurance method formulates ways in which the chance of producing a defected or low quality product is nearly finished. E.g. in a car manufacturing firm, the quality assurance department would make sure that all the raw material such as leather, steel, rubber, cotton etc which is being delivered by suppliers is of a good quality or not. Similarly, once all raw materials have been received, the task force which would use these materials would be checked too. Are they qualified enough to carry out this task? Is it motivated? Motivation needs to be accounted for importantly since it would lead to more efficient usage of resources. The Quality assurance department would also inspect the machines and tools that would be used. If these are available in good conditions than the work be done easily and more quality built into the products. If the staff is not provided good enough tools than the outcome might not prove to be of such a high quality. Hence, in a net shell the quality assurance department would look into each and every aspect of the production process where the issue of quality might be involved. This means that not only output produced by the labors would be inspected, rather each and every material, machine, tools and even the human factor would be considered when efforts are being made by the Quality Assurance department to maintain and sustain quality. This type of quality improvement technique is more popular than its Japanese counterpart since it has been noted that employees feel demotivated when their performance is put into question by inspectors who job role compels them to raise questions here and there. (Pride et al, 2011)
In contrast to Quality Assurance, The Quality Control technique has been an old one which mostly unpopular in industry workers. Firstly, this technique only looks upon and accounts for output which means that the workforce is to be blamed if any faults or rejections arise. Secondly, this technique takes a lot of time and delays the production process. It is here, where the term Quality Assurance is sought after, since it regards it illogical to check for the defects in the end. Rather, the quality assurance aims to cancel out all such factors which might lead to downfall in the quality of products. It works in a more friendly way with the factory staff, and hence is considered friendlier, than the quality control methods. (Besterfield, 2009)
Another problem of the quality control technique is that it appoints quality control inspectors who are given salaries to find defects from the goods produced. Since, it is the inspector’s job to find defects, they manage to find a small defect here and there in the products, which, in normal circumstances, could have gone unnoticed by a regular customer. Sometimes, the defects might not take place at all, but the inspectors might be persuaded to reject them so that their job role remains satisfied. Secondly, even if these defects are genuine, the labor is mostly found to be devastated from these inspectors and mostly despise them due to prejudice. Hence, a mutual agreement between the main parties of the quality standardization process is not reached, which severely affects the quality again. (Aikens, 2005)
However, it is not true that Quality Assurance is always beneficial for businesses. According to Pride et al, (2011) a major bias in the employees of various organizations is that companies do not care about quality, rather than they regard quality as one which reaps great profits. Hence, higher quality for higher profit, and lower quality for cheap price phenomenon is followed and accepted. Quality Assurance department fail to make their status as prominent as the Quality Control departments, since they are lenient on terms with the production staff. The Quality Assurance programs are not given much weightier, and it is by the usage of specific powers and control that quality assurance programs are matched.
Also, it proves to be very hectic and a complicated procedure to interact with all the departments and staff and to build quality into every nook and corner. If experienced staff is not recruited in this department, the department might collapse at an overall level, or might be good for nothing.
The quality assurance team, would not be inspecting the products and accept or rejecting them like their quality control counter-parts used to do. However, they would also accompany the production staff randomly to make sure that the work is being carried out in line with the quality standards set by the organization. Also the staff would randomly check the finished products in order to counter check the level of quality being produced. This might well be appreciated by the work force, who would be revealed that no strict and hand to mouth procedures are being followed. (Bhote & Bhote, 2000)
Bhote & Bhote (2000) have mentioned in the debate of which one is better; the authors have noted that that taking out defects and rectifying them is a sensible thing to do. However, it would be more sensible to go after the causes and reasons of the defects and abolish them once for all, so that no needs for future rectification are needed. This would aid in optimal usage of resources as well as motivation of the production staff would felt valued if their products were not scrutinized. (Besterfield, 2009)The Quality Assurance program is one such way of rectifying errors. However, it must be noted that in the attempt of finding and exploring errors, reaching their points and then trying to eliminate them might take a considerable amount of time and resources. Hence, there should be a separate budget for quality assurance procedures which need to be introduced. Quality Control, on the other hand, could still be use if the work force is of a rigid nature which does not appreciate changes in the way management approaches them. If this is the case, than the company should hire quality inspectors and pay them salary to take out defects in the products which are being manufactured. Also, it might so happen that suitable changes in the working environment and production changes cannot be made, so again the Quality Control checks could be introduced again. (Dale, 2003)
To conclude, it can be said that there have been no established theories whereby one method of quality compliance can be deemed as accurate and correct. However, it must be noted that major companies such as Toyota, the car manufacturer, General Electric as well as General Motors’ are preferring Quality Assurance over Quality Control, since it attempts to remove defects from taking place at the first place.(Webber & Wallace, 2007)
Bibliography
Beckford, J., 2009, Quality: A critical introduction, New York: Routledge.
Webber, L., and Wallace, M., 2007, Quality Control For Dummiers, Hoboken: Wiley
Aikens, H., 2005, Quality: a corporate force: managing for excellence, Pearson: Prentice Hall.
Bhote R., and Bhote, K., 2000, World Class Quality, New York: Amacom
Dale, G., 2003, Managing Quality, Oxford: Blackwell
Besterfield, 2009, Quality Control, Person: Prentice Hall
Stebbing L., 1997, (Revised 2009), Quality Assuranc, Michigan: Elis Horwood
Pride et al, 2011, Business, Mason: Cengage.
Stuck with your Research Paper?
Get in touch with one of our experts for instant help!
Tags:
Time is precious
don’t waste it!
writing help!
Plagiarism-free
guarantee
Privacy
guarantee
Secure
checkout
Money back
guarantee
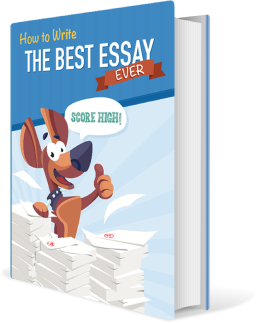