Disciplines
- MLA
- APA
- Master's
- Undergraduate
- High School
- PhD
- Harvard
- Biology
- Art
- Drama
- Movies
- Theatre
- Painting
- Music
- Architecture
- Dance
- Design
- History
- American History
- Asian History
- Literature
- Antique Literature
- American Literature
- Asian Literature
- Classic English Literature
- World Literature
- Creative Writing
- English
- Linguistics
- Law
- Criminal Justice
- Legal Issues
- Ethics
- Philosophy
- Religion
- Theology
- Anthropology
- Archaeology
- Economics
- Tourism
- Political Science
- World Affairs
- Psychology
- Sociology
- African-American Studies
- East European Studies
- Latin-American Studies
- Native-American Studies
- West European Studies
- Family and Consumer Science
- Social Issues
- Women and Gender Studies
- Social Work
- Natural Sciences
- Anatomy
- Zoology
- Ecology
- Chemistry
- Pharmacology
- Earth science
- Geography
- Geology
- Astronomy
- Physics
- Agriculture
- Agricultural Studies
- Computer Science
- Internet
- IT Management
- Web Design
- Mathematics
- Business
- Accounting
- Finance
- Investments
- Logistics
- Trade
- Management
- Marketing
- Engineering and Technology
- Engineering
- Technology
- Aeronautics
- Aviation
- Medicine and Health
- Alternative Medicine
- Healthcare
- Nursing
- Nutrition
- Communications and Media
- Advertising
- Communication Strategies
- Journalism
- Public Relations
- Education
- Educational Theories
- Pedagogy
- Teacher's Career
- Statistics
- Chicago/Turabian
- Nature
- Company Analysis
- Sport
- Paintings
- E-commerce
- Holocaust
- Education Theories
- Fashion
- Shakespeare
- Canadian Studies
- Science
- Food Safety
- Relation of Global Warming and Extreme Weather Condition
Paper Types
- Movie Review
- Essay
- Admission Essay
- Annotated Bibliography
- Application Essay
- Article Critique
- Article Review
- Article Writing
- Assessment
- Book Review
- Business Plan
- Business Proposal
- Capstone Project
- Case Study
- Coursework
- Cover Letter
- Creative Essay
- Dissertation
- Dissertation - Abstract
- Dissertation - Conclusion
- Dissertation - Discussion
- Dissertation - Hypothesis
- Dissertation - Introduction
- Dissertation - Literature
- Dissertation - Methodology
- Dissertation - Results
- GCSE Coursework
- Grant Proposal
- Admission Essay
- Annotated Bibliography
- Application Essay
- Article
- Article Critique
- Article Review
- Article Writing
- Assessment
- Book Review
- Business Plan
- Business Proposal
- Capstone Project
- Case Study
- Coursework
- Cover Letter
- Creative Essay
- Dissertation
- Dissertation - Abstract
- Dissertation - Conclusion
- Dissertation - Discussion
- Dissertation - Hypothesis
- Dissertation - Introduction
- Dissertation - Literature
- Dissertation - Methodology
- Dissertation - Results
- Essay
- GCSE Coursework
- Grant Proposal
- Interview
- Lab Report
- Literature Review
- Marketing Plan
- Math Problem
- Movie Analysis
- Movie Review
- Multiple Choice Quiz
- Online Quiz
- Outline
- Personal Statement
- Poem
- Power Point Presentation
- Power Point Presentation With Speaker Notes
- Questionnaire
- Quiz
- Reaction Paper
- Research Paper
- Research Proposal
- Resume
- Speech
- Statistics problem
- SWOT analysis
- Term Paper
- Thesis Paper
- Accounting
- Advertising
- Aeronautics
- African-American Studies
- Agricultural Studies
- Agriculture
- Alternative Medicine
- American History
- American Literature
- Anatomy
- Anthropology
- Antique Literature
- APA
- Archaeology
- Architecture
- Art
- Asian History
- Asian Literature
- Astronomy
- Aviation
- Biology
- Business
- Canadian Studies
- Chemistry
- Chicago/Turabian
- Classic English Literature
- Communication Strategies
- Communications and Media
- Company Analysis
- Computer Science
- Creative Writing
- Criminal Justice
- Dance
- Design
- Drama
- E-commerce
- Earth science
- East European Studies
- Ecology
- Economics
- Education
- Education Theories
- Educational Theories
- Engineering
- Engineering and Technology
- English
- Ethics
- Family and Consumer Science
- Fashion
- Finance
- Food Safety
- Geography
- Geology
- Harvard
- Healthcare
- High School
- History
- Holocaust
- Internet
- Investments
- IT Management
- Journalism
- Latin-American Studies
- Law
- Legal Issues
- Linguistics
- Literature
- Logistics
- Management
- Marketing
- Master's
- Mathematics
- Medicine and Health
- MLA
- Movies
- Music
- Native-American Studies
- Natural Sciences
- Nature
- Nursing
- Nutrition
- Painting
- Paintings
- Pedagogy
- Pharmacology
- PhD
- Philosophy
- Physics
- Political Science
- Psychology
- Public Relations
- Relation of Global Warming and Extreme Weather Condition
- Religion
- Science
- Shakespeare
- Social Issues
- Social Work
- Sociology
- Sport
- Statistics
- Teacher's Career
- Technology
- Theatre
- Theology
- Tourism
- Trade
- Undergraduate
- Web Design
- West European Studies
- Women and Gender Studies
- World Affairs
- World Literature
- Zoology
Supply Chain Management at International Automotive, Case Study Example
Hire a Writer for Custom Case Study
Use 10% Off Discount: "custom10" in 1 Click 👇
You are free to use it as an inspiration or a source for your own work.
What do you believe has been the most difficult challenge for Salinas?
Paul Salinas had a lot of training and experience before he began working for International Automotive. He had spent several years in Germany where he went through phases of training on a weekly, monthly, and yearly basis. His training extended from administrative to, technical, business, and operational positions in manufacturing plants and supply chain management. His experience extended to the ability to speak in three languages, English, Spanish, and German. His qualifications along with extensive experience made him the perfect candidate to help to solve the supply chain problem at International Automotive. Salinas’s prime objective was to leading the plant out of the red, where they were monthly losing $1 million at a total of $12 million. The Supply chain was so important that the company defined it as, “the “strategic coordination of business functions within a business organization and throughout its supply chain for the purpose of integrating supply and demand management.”(Stevenson, 2009) Salinas was given plenty of objectives in order to regulate the supply chain management, shipment, packaging, and logistics.
Salinas faced several challenges in order to be successful in helping International Automotive out of the red. Outlined in the case study, Salinas’ greatest challenge centered on International Automotive Company’s employees at the time in which several of the employees had not yet reached the desired level of responsibility and work ethics.(Business Case, 2011) Even though through the acquisition of the company, the challenge was the company’s conforming to IAC’s business culture. They had currently went through two different company changes within a short period of time, and some were not willing to budge to the new changes being implemented. “Although the employees had adapted to IAC’s culture, Salinas could still sense a lack of loyalty to the company.”(Case Study, 2011) The problems not only included a resistance to the changes, but also in the key departments where the biggest problem arose, many of the employees lacked the proper qualifications that related to the job they needed to perform. The outdated strategies that included doing the orders by hand and, shipping internationally, and not knowing the correct packaging for shipments harmed the company. The new processes and systems that were implemented to replace the older and inefficient methods required extensive training in order for employees to be able to operate to the fullest capacity. IAC relied on the philosophy of transparency, they started with the bottom up and the top down approach to eliminating hierarchies and offices in order to create a more open atmosphere. However, the loyalty from the employees were lax, with errors in logistics, shipping, and management were harming operations. The challenges of getting all employees on board with the new methods of supply chain management, and philosophy of IAC was not being thoroughly integrated within all the departments. In order to effectively solve the problem continued dialogue, training, and systems for improvement need to be implemented in efforts to ensure continual improvements to all key departments within the supply chain management.
References
“SUPPLY CHAIN MANAGEMENT AT INTERNATIONAL AUTOMOTIVE.” Richard Ivey School of Business Foundation. (2011).
Stuck with your Case Study?
Get in touch with one of our experts for instant help!
Time is precious
don’t waste it!
writing help!
Plagiarism-free
guarantee
Privacy
guarantee
Secure
checkout
Money back
guarantee
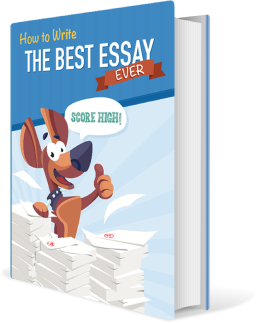